As downstream demand continues to soar, insulated gate bipolar transistor (IGBT), known as the “heart of power devices”, is facing an unprecedented shortage. Recently, several leading domestic manufacturers have also confirmed this situation, with many downstream customers adopting a long-term order locking supply strategy. Therefore, domestic manufacturers are urgently seeking new capacity expansion to alleviate overly strong market demand. Currently, several major foreign manufacturers, including Infineon and STMicroelectronics, have postponed IGBT delivery times of over 50 weeks. Faced with high scheduling congestion, these large factories are not in a hurry to expand production.
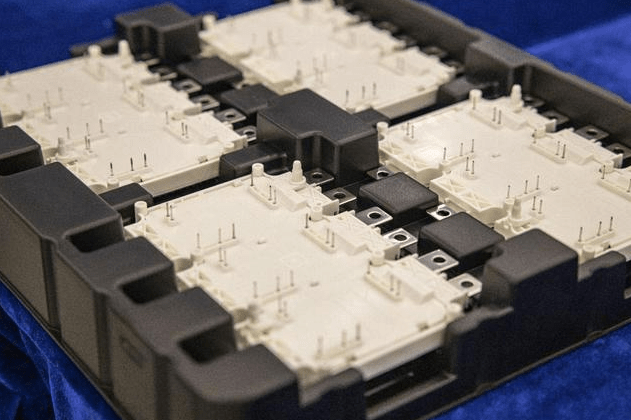
In the industry’s view, the supply of IGBT has been continuously tight since last year, and there have been no signs of slowing down so far. Moreover, although domestic manufacturers are eager to expand production, the line construction cycle is generally more than two years, and it is expected that the supply and demand mismatch will be difficult to solve before 2025.
IGBT has excellent performance such as high frequency, high voltage, high current, and easy switching. It is known as the “CPU” of power electronic devices and the “chip” of new energy in the industry. The reason why electric vehicles can beat fuel vehicles with acceleration is related to the role of this “heart”.
Industrial control and new energy vehicles are the two downstream areas with the largest demand for IGBT. According to statistics in 2021, these two major areas account for 37% and 28% respectively, followed by the new energy power generation and home appliance frequency conversion markets, with demand accounting for 9% and 8% respectively. Especially since 2020, the demand for new energy vehicles has significantly increased, up 19%, making it the main source of incremental demand for IGBT.
Industry analysis shows that there are two main reasons for the large shortage of IGBT. Firstly, the proportion of current photovoltaic inverters using IGBT has significantly increased; Secondly, the semiconductor industry is currently in adjustment, with limited production capacity and many capacity being taken away by new energy vehicle manufacturers. Tesla has also been adding fuel to the fire recently. On March 1, Tesla publicly announced that it would slash the use of silicon carbide by 75% in its electric vehicles. The industry assumed that the demand for IGBT, one of the alternative solutions, will skyrocket.
This situation has been confirmed by domestic manufacturers. Major industry player Zhuzhou CRRC Time Electric recently observed strong demand for IGBT, and many important customers have chosen to sign a three-year contract (2024-2026). The company urgently needs new production capacity for IGBT Phase III to alleviate the overly strong market demand. The company revealed that many car manufacturers have collaborated with the company to develop new solutions, which may increase the application of silicon based IGBT.
Generally speaking, an electric vehicle uses hundreds of IGBTs, which is seven to ten times more than traditional fuel powered vehicles. Currently, the orders for domestic vehicle grade IGBTs within the year are mostly secured. The occurrence of this situation is directly related to the fact that international large factories are not in a hurry to expand production. From the perspective of the industry, overseas large factories have a relatively conservative attitude towards expanding IGBT production and are unable to meet market demand in a timely manner, giving domestic enterprises an opportunity to take advantage of it.
A research report from EASEC pointed out that seen from global market competition, European, American and Japanese manufacturers have strong financial strength, leading technologies, and rich industry experience, which helped them seize the vast majority of the global market share of power semiconductors and have always maintained a significant leading advantage.
Manufacturers such as Infineon, Mitsubishi, and Fuji Electric have contributed over 80% of global production capacity. However, domestic manufacturers do not have an advantage in global competition and have a low market share, with a localization rate of less than 20%. However, due to the slow iteration of IGBT product updates, local manufacturers are given time to catch up on technology. According to the Infineon’s financial report in 2021, the global market share of Hangzhou Silan Microelectronics in IGBT single tube and IPM reached 3.5% and 2.2%, both ranking eighth in the world, while StarPower has a market share of 3.0% in the global IGBT module market, ranking sixth in the world.
The expansion of IGBT production from 2021-2023 will be led by Chinese manufacturers. They will take advantage of this opportunity to successfully enter downstream customers through low prices, timely customer service, and stable supply chains, and gradually increase production capacity to increase market share.
BYD has already invested in the construction of a power semiconductor production capacity project in Jinan, with a total scale of approximately RMB 4.9 billion yuan. BYD has previously stated that in the face of continuous growth in the new energy vehicle industry, the new wafer production capacity is still far from meeting downstream demand. Thus in the short term, it is difficult to change the mismatch between domestic supply and demand, and the situation may continue until 2025.