In the context of the rapid rise of global renewable energy, photovoltaic (PV) power generation is increasingly becoming a powerhouse in the energy sector. While primary materials have received widespread attention, auxiliary materials such as photovoltaic glass, frames, encapsulants, and silver paste also play a crucial role. These auxiliary materials not only directly affect the performance and lifespan of PV modules but also provide essential support in ensuring the stability and efficiency of PV systems.
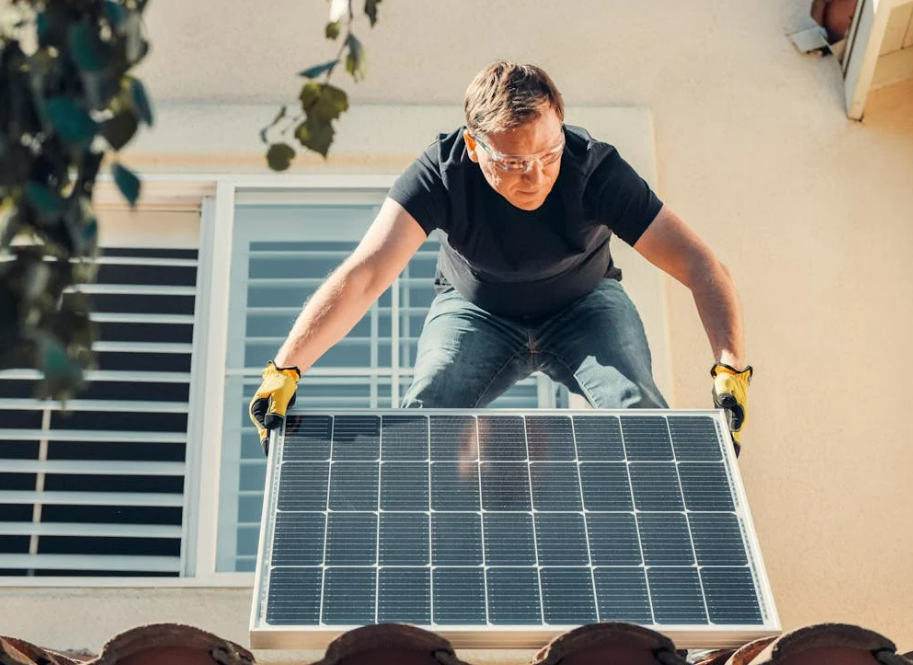
As the PV industry rapidly develops, the market for auxiliary materials is also changing. Research and development of efficient materials, the introduction of customized products, and strategic sourcing have become critical for companies and investors in the PV sector. Understanding the market dynamics and future trends of these key auxiliary materials is now essential for success.
According to InfoLink Consulting’s “Photovoltaic Auxiliary Material Supply and Demand Analysis Report,” the cost structure of the PV supply chain has undergone significant changes since 2023. For instance, data from September 2023 for TOPCon monocrystalline modules indicates that silicon materials accounted for 15%, glass for 11%, and frames for 10% of production costs, with silicon materials representing a substantial portion. However, as silicon prices continue to decline in 2024, the cost structure of the PV industry has shifted noticeably. By September 2024, the cost proportion of silicon materials has dropped to around 8%, while the shares of auxiliary materials, including photovoltaic glass at 13%, frames at 13%, and silver paste at 11%, have been rising. The total share of eight major auxiliary materials has increased from 48% in September 2023 to about 57% in September 2024.
This trend reflects an overall decline in industry prices. Since 2024, the overall prices within the PV supply chain have decreased significantly compared to previous years, compressing profit margins across various segments and prompting manufacturers to seek new ways to reduce costs and enhance efficiency. As silicon prices fall, the importance of the price and quality of auxiliary materials, which are indispensable in modules, has become increasingly prominent. To maintain a competitive edge in a fierce market, many PV manufacturers are allocating more resources and R&D efforts toward optimizing auxiliary materials through new material applications, process improvements, and supply chain optimization.
Looking ahead, as silicon prices stabilize, auxiliary materials will continue to play an increasingly important role in PV module production costs. To cope with intensifying market competition, companies will focus more on cost control and performance optimization of auxiliary materials. This approach not only enhances overall production efficiency but also improves the market competitiveness and profitability of the modules. Overall, photovoltaic auxiliary materials are becoming a key link in reducing costs and enhancing efficiency within the PV supply chain, driving the entire industry towards a more efficient, economical, and sustainable future.
Amid the rapid expansion of the global PV market, the overseas layout of auxiliary material companies has become an important trend in industry development. With growing demand for clean energy in regions like Europe, North America, Asia, and the Middle East, the global supply chain and production bases for PV auxiliary materials are gradually improving. As a major production base for these materials, many Chinese companies have expanded their capacities overseas, primarily targeting Southeast Asia, particularly the four ASEAN countries, to navigate foreign trade policies, reduce logistics costs, shorten supply cycles, and seize local market growth opportunities. Additionally, local manufacturers from India and South Korea also maintain a presence in the auxiliary material market.
In Southeast Asia, taking advantage of the region’s labor cost benefits, an increasing number of Chinese PV auxiliary material companies are establishing factories due to the growing demand for these materials alongside the expansion of primary material companies. This development is creating an ecosystem that complements local PV module manufacturing, while also encouraging firms to strengthen the export and local production of key auxiliary materials. This response addresses changes in U.S. market policies and aligns with local compliance and incentive requirements. In particular, one condition for exemption from anti-circumvention measures is the use of Southeast Asian modules containing at least four of six auxiliary materials (silver paste, aluminum frames, glass, back sheets, encapsulants, junction boxes) that are not sourced from China, thereby meeting the needs of primary material customers for U.S. exports.
Overall, through globalized layouts, PV auxiliary material companies are not only enhancing their ability to withstand supply chain risks and meet the needs of primary material customers but also promoting global collaboration in technological innovation, laying a solid foundation for future market expansion.