In recent years, with the rapid development of artificial intelligence (AI), industrial Internet, big data and other information technologies, the solar industry has become more and more digital and intelligent. At the beginning of 2022, five departments including the Ministry of Industry and Information Technology jointly issued the Action Plan for Innovation and Development of Intelligent Solar Industry (2021-2025), which proposed building an intelligent solar industry ecosystem.
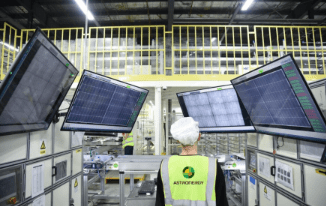
Chint has always been the pioneer and practitioner of smart manufacturing in China. As early as 2016, Chint built the world’s first solar manufacturing+Internet transparent factory and later introduced advanced automatic production lines, independently developed MES systems, and introduced AI automatic detection of EL defects for the first time in the industry.
In the process flow of solar cells and modules, almost every key link is accompanied by a quality inspection to ensure the high quality. For modules, the quality inspection runs through from the cells to the final module finished products, as well as special attention for some key links including appearance and internal defects.
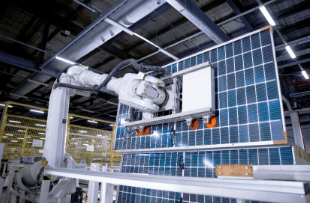
Previously, the detection process is usually realized by manual visual inspection, which wastes too much time and labor together with high cost, not to mention the rising undetected error rate. The AI detection provides a powerful tool with more efficiency and accuracy for the solar detection process.
AI detection, in short, is to put a cell and module under the camera connected to the computer for shooting, and let the computer detect and analyze the image to identify whether the product has defects. Chint has cooperated with Alibaba Cloud in 2018, and introduced AI automatic detection of EL defects in the industry for the first time with the help of AI image quality inspection technology, and successfully applied it to all base factories of Chint.
AI detection is based on AI deep learning algorithm, which integrates algorithm integration, model training, model deployment and detection output, and can intelligently identify and determine common defect types of cell modules. AI detection in the solar industry can generally be divided into appearance AI detection and EL AI detection, which can be simply understood as the technology of detecting the external and internal defects of the cell module.
External detection is an intelligent detection for the appearance of cell modules, which can accurately identify eight common defects such as foreign body, welding displacement, bubbles, and detect whether the semi-finished products meet the set standards. In addition, it can almost achieve zero missing detection in identifying the module spacing and creep age distance.
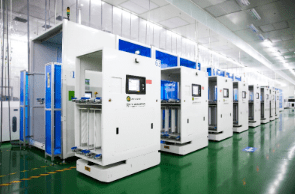
At present, Chint’s online intelligent detection coverage rate of cell can reach 72%, over 98% of accuracy. The module end includes detection such as serial detection, semi-products, finished products, glue filling, frame, boxing, nameplate, etc, with intelligent inspection coverage rate of 92% and 99.7% of accuracy. However, only few enterprises in the industry can achieve intelligent detection coverage rate of over 90%.
Each solar module produced by Chint can be placed with a barcode, like an ‘ID card’, as the only identifiable code of this module for life.
From the beginning of production, the code is injected by laser, and it is automatically scanned by the online code scanner before entering each process. Meanwhile, the MES independently developed by Chint adjusts the corresponding process parameters and selects the corresponding raw materials for production according to the preset material information of the work order. Each process of subsequent module production will be carried out under the path set by the work order. After the product leaves the factory, users can trace the whole process information of the product from raw materials to process and equipment, and then to delivery time and configuration parameters by scanning the barcode of the product, so as to realize the traceability of the whole life cycle.
Unlike the full assembly line operation of the module workshop, the process flow of the solar cell workshop is more independent. The process flow is not transferred from one machine to the next, but needs to be cached after the end of one process, and then transported to the next process, which means a lot of material handling needs.
In traditional workshops, the machines and equipment for production and manufacturing are often highly numerically controlled, whilst there is no better solution for the material handling and it’s usually carried by manual handling. To effectively improve the efficiency, Chint introduced Automated Guided Vehicle (AGV) in the cell workshop in 2022, realizing the automation of the whole workshop handling.
In order to meet the daily transportation and distribution requirements of millions of solar cells, Chint’s Haining Base is equipped with 226 AGVs, which are equipped with 93 automatic charging piles. All cars are managed and dispatched by the central management system. The central management system automatically schedules the AGV to carry out the handling task by matching the requirements of the previous and subsequent processes. After the car picks up the silicon wafer from the task position, it takes it to the next for processing. AGV covers all automatic supply and distribution of materials.